LW系列卧式螺旋卸料沉降离心机
一、概述
卧式螺旋卸料沉降离心机是一种利用离心力分离不同密度介质的连续高效分离设备。可用于液相与固相、不同比重液相分离,适应能力广,处理能力大,出渣含湿率低,可连续处理所以自动化程度高;且整机占地面积小,工作噪音低,电耗低节能效果明显。产品已广泛应用于食品、化工、石油、制药、选矿、煤炭、水处理和船舶等行业。
本公司生产的离心机主要是卧式螺旋卸料离心机,可以对粒径几微米至3毫米范围内固体颗粒的悬浮液进行浓缩、脱水或分级分离。1998年由国家环保总局批准列入《一九九八年国家环保****实用技术推广计划》项目。
现有LW(逆流式)、LWB(并流式)、LWS(三相分离式)三个系列共20余种规格及污泥浓缩离心脱水一体机。
我公司成立以来,不断消化吸收国内外先进技术,同时积累经验不断创新。立足于市政、工业污水的处理,同时成功进入蛋白萃取分离以及酒精分离、果汁分离等多个行业。
二、工作原理
悬浮液从进料管进入卧螺离心机,在转鼓的高速旋转下,比重大的固体被甩向转鼓壁,比重轻的液体被挤向转鼓中心。在螺旋和转鼓的差转速作用下,沉降到转鼓壁上的固体被螺旋输送器推向转鼓小端出渣口,排出机外,液体通过转鼓大端溢流孔排出机外。
三、大规格高分离因素卧式螺旋卸料沉降离心机
(1)该系列卧螺离心机分离因素可达4000G,对物料适应性广,捕抓水中悬浮颗粒直径处于5μm~100μm范围的悬浮液都可以分离,转鼓直径Φ500mm卧式螺旋离心机处理市政污水可达到35-40M3/h。
(2)能源消耗低,处理量大,也能节约大量的占地面积。
(3)广泛适用于大豆蛋白,鱼蛋白和海藻蛋白的分离工序。
(4)生产自动化程序高。可实现完全自动化,改善劳动环境,提高生产率。
四、主要部件
1、转鼓:
转鼓采用不锈钢材质制作而成,固渣排放口采用360度可更换的耐磨套,转鼓内表面按物流方向装有纵向筋条以保护内表面不被磨损。
2、螺旋推料器:
螺旋芯管及叶片采用不锈钢材质制作而成,螺旋推料器简体布料孔采用分段的形式圆弧形出口,螺旋的出口也采用纳米金刚玉镶套。
3、行星齿轮差速器
渐开线行星齿轮差速器,以速差和扭矩模式运行。
4、耐磨防护:
a、锥转鼓排渣口的耐磨采用镶嵌可更换的耐磨套,纳米金刚玉(陶瓷)衬套。
b、转鼓壁的防护,在转鼓内表面按周向等分地装焊厚度适当的筋条。
c、在螺旋外缘镶焊硬质合金耐磨块或堆焊德国进口GN-W2C碳化钨。
5、轴承及润滑:
设备的整个旋转单元由两个主轴承支撑。轴承的设计寿命在L10标准下达100,000小时。
6、驱动系统:
主驱动系统(转鼓):采用电机-转鼓皮带轮-窄V皮带-变频器与传动部件组成,采用软启动装置方式。
辅驱动系统(螺旋输送器):采用行星齿轮系统-螺旋输送器-电机-变频器与传动部件组成的驱动系统。
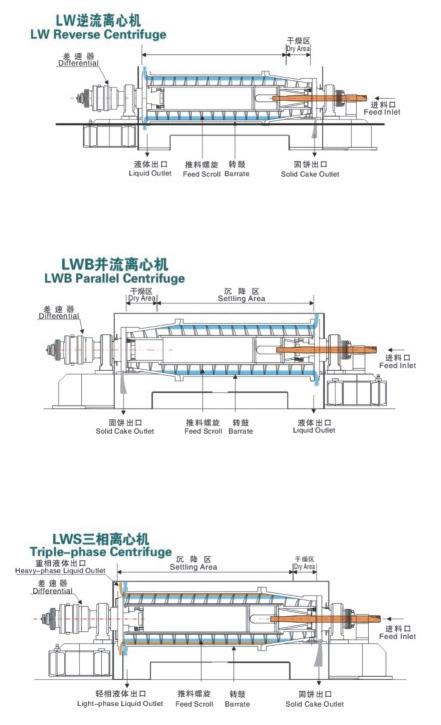
五、技术特点
1、在螺旋叶片镶焊耐磨合金片,这样大大的增强了螺旋的耐磨性能。镶焊耐磨合金片的螺旋使用寿命一般在20000小时以上。广泛适应市政污水和矿产物料的分离工作。
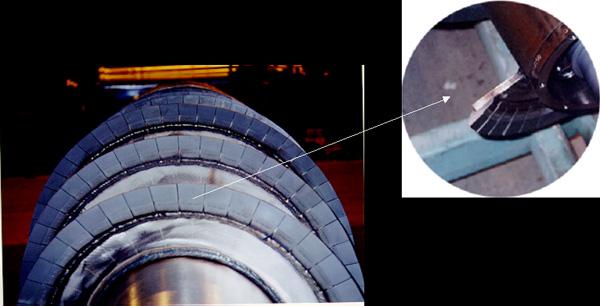
2、在螺旋进料口采用可更换的圆弧形耐磨材料,减轻了进料口局部的磨损。
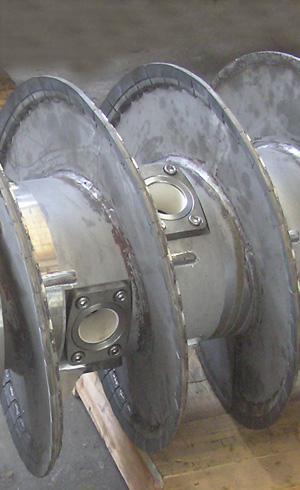
3、在离心机转鼓的排渣口镶嵌耐磨合金套。该合金套除了具有保护排渣口的抗磨损功能外,另有排料刮刀的作用,这样就大大增加了出渣口的使用寿命。
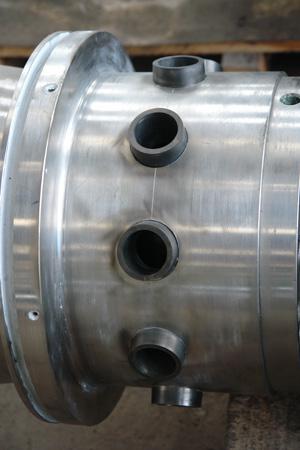
4、在转鼓内壁装焊保护筋条,使得转鼓与螺旋间的物料不会直接摩擦,从而大大减少了转鼓内壁磨损的可能,同时又提高螺旋器的输送效果,改善离心机的分离效果。

5、采用大锥角加缓冲板的先进技术转鼓锥段采用大锥角,加长了沉降区长度,就提高了离心机的沉降能力12%。增加缓冲板,使离心机能在超液池深度的状况下工作,增加沉降能力15%。综合这两项,离心机的沉降能力就会提高28.8%。采用大锥角,沉渣在转鼓内受到二次的挤压,沉渣的含水率会进一步降低。
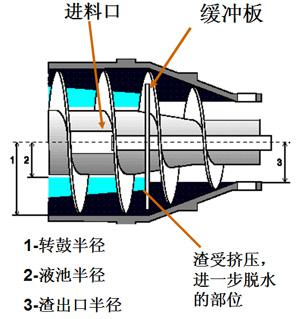
6、转鼓采用大长径比结构。长径比可达4以上,加长了沉降去,提高了分离效果与处理能力。
7、镂空式螺旋叶片设计,该设计使得液层大大地减少了对固体层的扰动。在保证污泥回收率的前提下,相对提高出泥的干度;在保证出泥干度的情况下提高了污泥的回收率。
8、背驱动装置系统。自动调节差转速(根据物料浓度及流量变化,导致螺旋力矩的变化,背驱动装置连续不断的根据PLC、计算出变化的力矩,改变副电机的转速,实现自动调节改变差速),以保证泥饼的恒干度。根据物料情况,背驱动装置,改变旋转方向,实现正转及反转功能。转鼓内物料的堆积,背驱动装置实现反转,这时差速很大,使堆积在转鼓内的物料容易排出。
六、技术参考指标
处理量:0.5~80m3/h;进料浓度:0.5~35%;长径比:2.4~5;噪音:≤85dB(A);固体回收率:≥95%;出渣含水量:≤75%;分离因数:1500~4000
离心机参数表
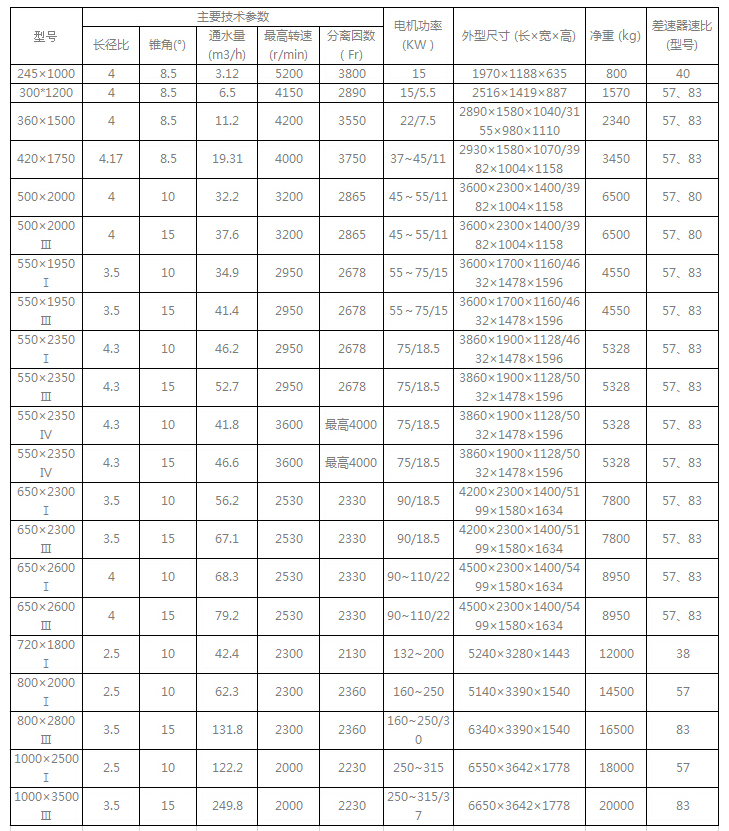
注:1.通水量是指被分离的物料在离心机转鼓内平均停留时间在20秒时的通过流量;
2.外形尺寸一栏中符号“/”前的数据是指电机与离心机主机水平放置时的外形尺寸,符号“/”后的数据是指电机与离心机主机垂直放置时的外形尺寸,后者比前者占地减少20%~50%;
3.****转速与分离因数一栏中符号“/”后的数据是指用高强度钢制造的转鼓能达到的转速与分离因数;
4.工作转速根据用户实际情况设定。
5.同一机型根据其电机安装形式分为电机在转鼓同一水平面安装。当转鼓直径≥550时,建议采用垂直安装可节约大量占地面积。
6.转鼓直径相同,转鼓长度较长用于有机物含量较高物料;转鼓长度较短用于无机物含量较高的物料。
绿水离心机显著特点
一、采用双电机双变频控制,其优点耗能较小。因为双电机双变频控制,当辅电机滞后时为发电机工作状态,辅电机将动能转换电能,通过共母线反馈给主变频器,耗能下降,一般节约能耗10%左右;
二、我公司卧螺离心机采用双电机双变频工作方式与液压差速器比较,具有如下优点:
1)综合能源消耗降低,除了电机转换效率损失减少以外,还减少油泵液压站的油耗和冷却水消耗;
2)没有油料和水的跑冒点漏,减少污染环境;
3)双电机双变频操作方便,结构简单,故障几率大大减少;
4)离心机一旦发生堵料现象,双电机双变频只要通过电机正反转即可排除,反应速度只要100~150ms,而且现在通过PLC设置恒扭矩控制,发生堵料死机的几率也大大减少,当电机扭矩加大,电流升高时,PLC立即做出反应,降低辅机转速增大差转速加快排泥或降低进料泵的转速减小进料量,避免发生堵料死机的现象。
5)双电机双变频的差转速控制高达5~70rpm,适应范围广;而液压差速器的差转速调速范围只有0~20rpm。
三、我公司制造的离心机大规格高分离因素是一个很大特点:LW550以下离心机的分离因素高达4000G;在污泥脱水时分离因素只要2800G左右,我们离心机在较低速条件下运行,更加稳定可靠,减少机件磨损,寿命延长。
四、我们公司离心机的螺旋推料器的周边采用等离子镶焊硬质合金片比喷焊GN-W2C其耐磨性能提高一倍还多。比用螺钉机械固定也要可靠很多,高速旋转条件下不容易掉片和断裂。
五、我们离心机螺旋推料器的芯管布料孔采用分段圆弧出料口,其剖面是圆弧形,分段进料口减少了物料对螺旋叶片的直接冲刷,减少磨损,使螺旋推料器长时间地安全运行。螺旋推料器在制造过程中增加了时效处理和电脑动平衡自动配重新工艺,从而提高了产品的整体结构稳定性能和提高工作寿命。
六、我们离心机转鼓的出料口镶嵌纳米锆刚玉(陶瓷),镶套提高耐磨性,而且一旦发生局部磨损只要卸下来反转过来装上去再使用,再装上去又可以使用很长一段时间,整体使用寿命大大提高。转鼓材料采用2205双相不锈钢,整体离心浇铸而成,其强度耐腐蚀性能有了极大的提升。
七、我们离心机螺旋采用圆柱滚子轴承加推力球轴承相组合,与其他单位采用角接触球轴承相组合其轴向推力提高了20%,提高了轴承承载能力和产品运行的可靠性。
八、我们离心机的差速器采用二级渐开线行星齿轮差速器,运行平稳,体积小,又采用高精度硬齿齿面磨齿齿轮,通过精心设计,使其具有足够的接触强度和抗弯强度,以满足传递大扭矩需要;为提高齿轮使用寿命,加大行星齿轮传动系统的浮动量,使齿面啮合更加柔和,行星齿轮轴承采用承载力大并且稳定可靠的滑动轴承,该轴承采用高新材料和精细加工工艺,在接触压力达到20MPa时,还能保持正常工作。可以传递扭矩达到10×104N•m时不会失效。
九、我们公司离心机设计时采用大锥角双锥角加BD板,加长沉降区长度,提高处理能力,使清液出口更加清澈。在山东瑞泰纤维素分离时,我公司离心机出液口清液通过透光率测定达到76%,而苏州某公司离心机的出液透光率只有38%,我公司离心机漏料很小为用户提高材料利用率增加效益。我们公司LW420×1750离心机2004年3月安装在浙江义乌水处理中心进行运行时,离心机每小时处理量为25m3/h(进料浓度4.9%情况下),正常运行一直稳定在23~25m3/h以上,稳定运行五年以上。
十、我们离心机转鼓出料口采用斜向切口,使排出固相减少阻力,做到永不磨损。
十一、污水处理厂的污泥在脱水过程中原来贮存在污泥中的硫化氢、硫脲、硫醇之类的恶臭气体,在分离浓缩过程中随分离液排出来,散发在脱水间污染工作环境,影响操作者身心健康。我们公司随离心机配置一只气液分离器,分离液排出来通过气液分离器将恶臭气体分离出来,排出窗外或提供除臭处理,洁净了工作环境。